In today's fast-paced and ever-evolving work environment, safety remains a paramount concern across all industries. Safe handling training is an essential program designed to educate employees on the proper techniques and procedures for handling materials, equipment, and hazardous substances safely. This training not only prevents workplace injuries but also promotes efficiency and productivity by fostering a culture of safety and awareness.
The Importance of Safe Handling Training
Safe handling training is crucial for several reasons:
- Preventing Injuries and Accidents: Many workplace injuries are a result of improper handling of materials or equipment. Training employees on the correct methods to lift, carry, and move objects significantly reduces the risk of musculoskeletal injuries, cuts, burns, and other accidents.
- Compliance with Regulations: Various regulatory bodies, such as the Occupational Safety and Health Administration (OSHA) in the United States, mandate specific safety standards that employers must adhere to. Safe handling training helps ensure that organizations comply with these regulations, thereby avoiding legal penalties and fines.
- Enhancing Productivity: A safe work environment leads to fewer accidents and injuries, which means less downtime and absenteeism. Employees who feel safe are more likely to be productive and engaged in their work.
- Promoting a Safety Culture: Safe handling training fosters a culture of safety within the organization. When employees are aware of the importance of safety and are trained to follow best practices, they are more likely to look out for themselves and their colleagues.
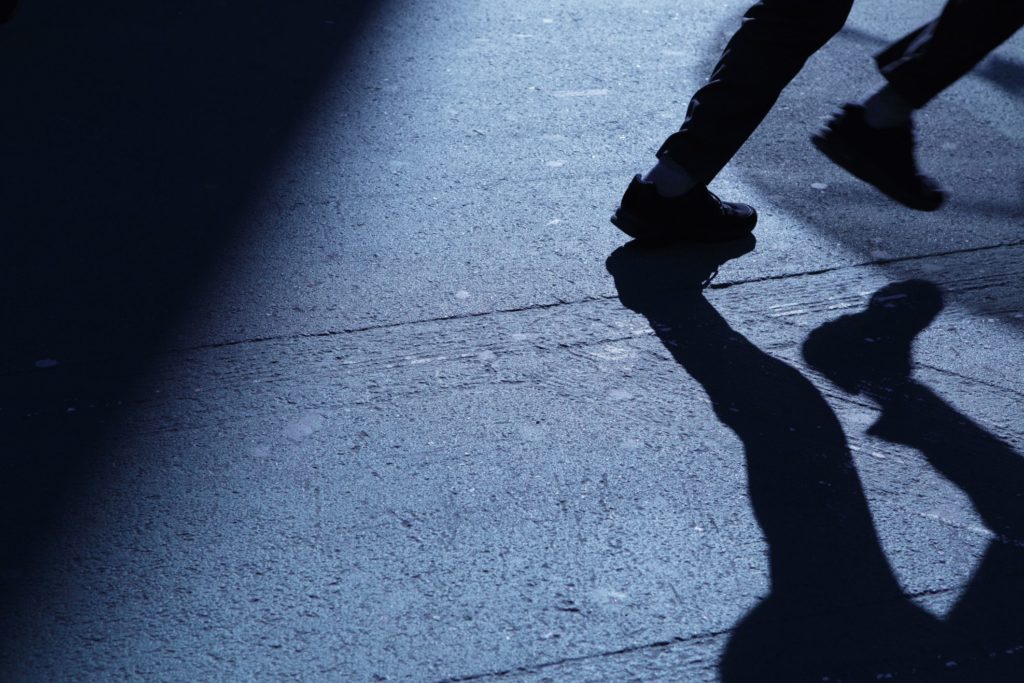
Key Components of Safe Handling Training
Effective safe handling training programs typically include the following components:
- Risk Assessment: Identifying potential hazards in the workplace is the first step in developing a comprehensive training program. This involves evaluating the types of materials and equipment used, as well as the tasks performed by employees.
- Proper Lifting Techniques: Employees should be trained on the correct lifting techniques to avoid back injuries and strains. This includes using their legs to lift, keeping the load close to their body, and avoiding twisting movements.
- Use of Personal Protective Equipment (PPE): Training should cover the appropriate use of PPE, such as gloves, safety goggles, and helmets, to protect employees from potential hazards.
- Handling Hazardous Materials: Employees should be educated on the proper procedures for handling hazardous materials, including the use of Material Safety Data Sheets (MSDS), proper storage, and disposal methods.
- Ergonomics: Training should address ergonomic principles to ensure that workstations are designed to minimize strain and injury. This includes proper posture, workstation setup, and the use of ergonomic tools and equipment.
- Emergency Procedures: Employees should be trained on the appropriate actions to take in the event of an emergency, such as spills, fires, or equipment malfunctions. This includes knowing the location of emergency exits, first aid kits, and fire extinguishers.
Implementing Safe Handling Training
To implement an effective safe handling training program, organizations should follow these steps:
- Assess Training Needs: Conduct a thorough assessment of the workplace to identify specific training needs based on the tasks performed and the hazards present.
- Develop Training Materials: Create comprehensive training materials that cover all aspects of safe handling. This may include instructional videos, manuals, and hands-on demonstrations.